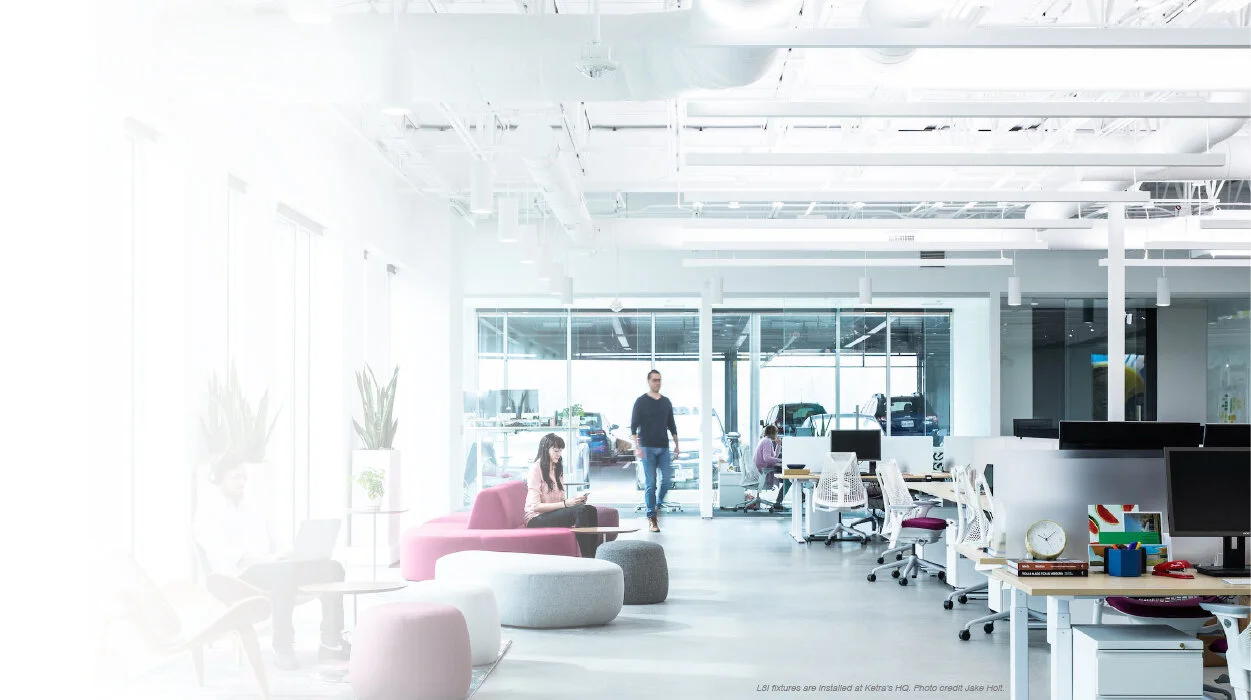
Developing a new product family:
A linear pendant lighting system
Product design and development
Photo by Jake Holt
I led the design and development of this highly customizable, aesthetically invisible pendant lighting product family.
I can draw several parallels between designing products at Ketra and using service design methods now. I was responsible for both front of the house design — understanding the market needs and translating them into tangible features — as well as back of the house processes — like understanding and developing the supply chain — for getting the products assembled, boxed up, and shipped as specified by our customers.
Ketra is an LED lighting and controls company based in Austin, TX specializing in architectural and residential applications. I spent two years working there as a mechanical engineer in new product research and development. In a startup environment, I wore many hats that included designing parts and assemblies, developing manufacturing processes, liaising with internal and external stakeholders, and occasionally tagging along on field visits.
My role: Lead mechanical design engineer
KEY CHALLENGE
Managing SKU complexity
This product required flexibility for customization including size, configuration, color, voltage, type of joinery, and ceiling mounting accessories among others. Modularization, attention to detail, and cross-discipline communication were critical to getting this right.
KEY CHALLENGE
Designing for in-field joining and wiring
A core feature of this product is joining end-to-end for long continuous runs and to make geometric shapes. As a premium lighting product with a simple rectilinear housing, attention to details like aligned connections and no ‘light leak’ were critical.
The solution was developed through an iterative process. Installers would be potentially connecting dozens of fixtures on a chaotic job site, so the mechanism had to be robust, simple to use, and efficient to manufacture.
KEY CHALLENGE
Developing the assembly line
As we transitioned to production, my job shifted to working with our CM to dial in and approve parts as well as setting up final assembly in our Austin warehouse. This included designing and making assembly jigs, creating instructional guides, and training assembly workers, supervisors, and managers on the process.
TRANSLATING THIS WORK TO SERVICE DESIGN
I can draw several parallels between designing products at Ketra and using service design methods now. I was responsible for both front of the house needs — understanding the market needs and translating them into tangible features — as well as back of the house processes — like understanding and developing the supply chain — for getting the products assembled, boxed up, and shipped as specified by our customers.